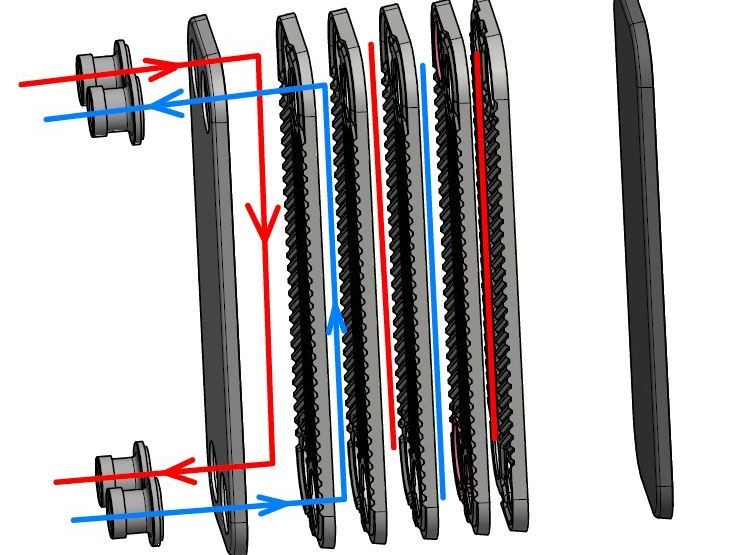
Funzionamento scambiatori di calore a piastre : scambio termico monofase e bifase
Gli scambiatori di calore a piastre hanno lo scopo di riscaldare/raffreddare fluidi di processo (monofase ad esempio acqua, olio, glicole, ecc) oppure nel campo bifase quello di fungere da evaporatore o condensatore (utilizzando fluidi frigorigeni come R134a, R1234ze, R410A, ecc. ) in un ciclo frigorifero a compressione di vapore.
In questo articolo cercheremo di spiegare in modo semplice il funzionamento di questi tipi di scambiatori.
Brazed plate heat exchangers: single-phase and two-phase
Plate heat exchangers have the general purpose of heating / cooling process fluids (for example water, oil, glycol, etc.)
In the two-phase field they are used as evaporator or condenser (using refrigerant fluids such as R134a, R1234ze, R410A, etc.) in a vapor compression refrigeration cycle.
In this article we will try to explain in simple way these types of heat exchangers.
In the case of a single-phase process we have two fluids that enter the heat exchanger generating a perfect countercurrent flow, therefore, the hypothetical maximum outlet temperature of both fluids will be equal to the inlet temperature of the opposite fluid.
This could only happen if the exchange area tended to infinity, so in reality this cannot happen.
So let’s see an example of a single-phase countercurrent flow, in which the cold fluid (in blue) enters and increases his temperature removing heat from the hot fluid (red) which is going to cool down, decreasing its temperature
In the case of a plate heat exchangers evaporator, in general, the purpose is to cool down a process fluid by evaporating a refrigerant fluid at constant temperature.
By far the most common application is to cool water from 12 ° C to 7 ° C for air conditioning systems.
In this plate heat exchanger, the refrigerant fluid enters in liquid phase at high speed (in reality the inlet vapor quality goes from 0.2 to 0.3) and evaporates through the plate exchanger from the bottom upwards, removing heat from the fluid that flows on the other side.
The last part of the exchanger is used to overheat the already evaporated gas so that there is no return of liquid particles in the compressor to avoid breakage of the compressor itself.
The most important part of this process of evaporation is the correct distribution of the two-phase fluid at the inlet of the heat exchanger.
The target is to introduce the same gas flow rate in every channel of the heat exchanger along all the package of plates.
Onda has patented a distribution system that allows gas to be distributed homogeneously along the entire exchanger.
As we can see in the figure, it can be seen that a correct distribution has a homogeneous overheating zone of the gas (in orange) from the beginning to the end of the exchanger.
If the distribution is not homogeneous we will have areas with more superheated steam and areas with less superheated steam, the operation of the chiller in this case may be unstable.
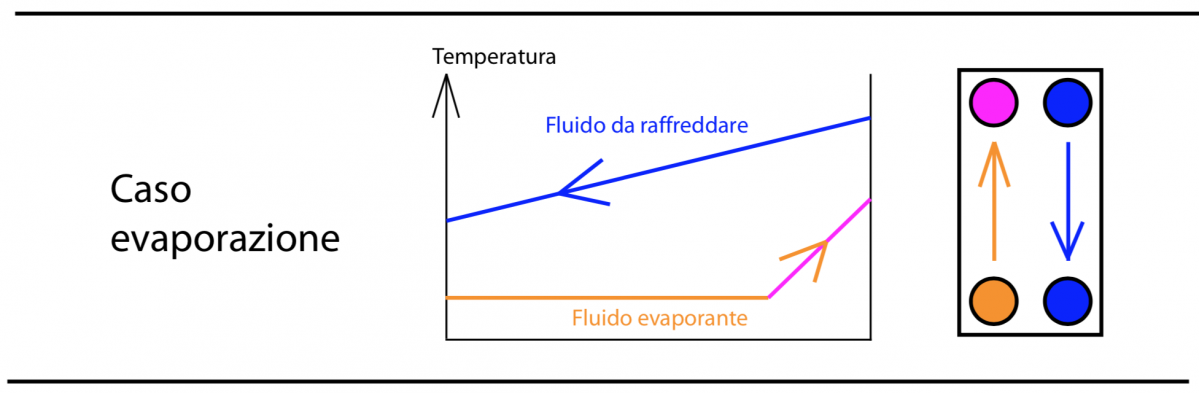
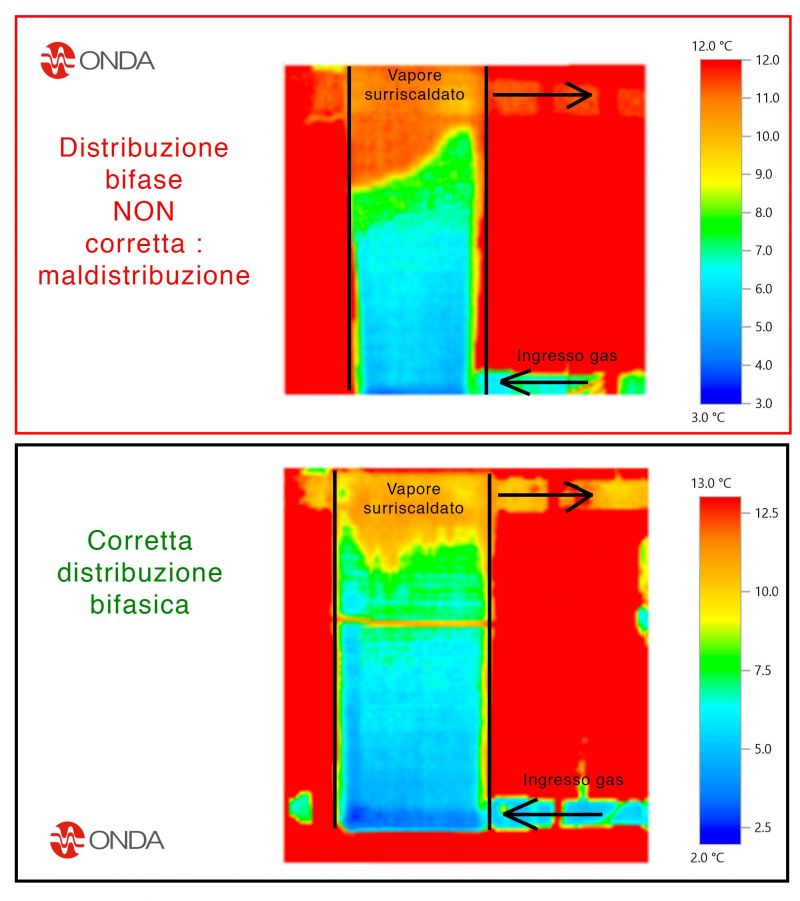
In the last case of brazed plate heat exchangers condenser, on the other hand, we have a refrigerant fluid in a gaseous state (generally at a high temperature about 60-70 °C) that condense at the expense of a fluid which, on the other side of the exchanger, is heating up.
In general the condensing temperature of the refrigerant is about 40°C and the fluid in the other side goes from 30 to 35°C.
The last part of the exchanger is used to subcooling the liquid condensate by a few degrees, usually 3-4°C.
In this case the superheated gas enters at the top and descends through the exchange plates, condensing until it becomes liquid and exiting at the bottom.
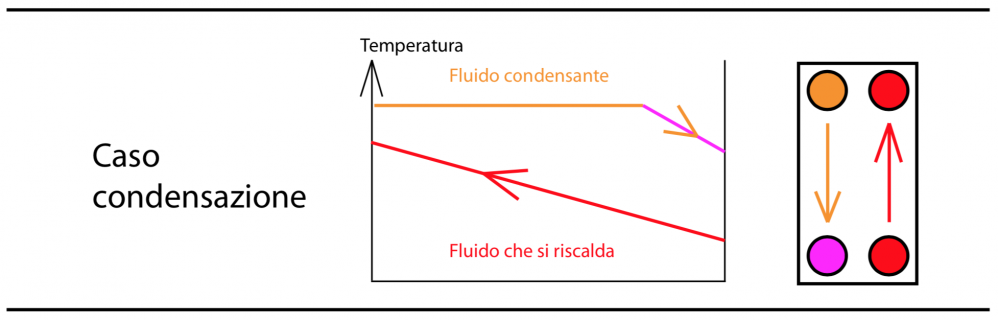
Enrico Golin
Wieland Onda Srl