Scambiatori di calore a piastre
Generalità
Gli scambiatori a piastre furono prodotti intorno agli anni ’20 e da allora hanno trovato un largo impiego in molti settori.
Lo scambiatore a piastre consiste in una serie di piastre parallele che vengono sovrapposte opportunamente permettendo la formazione di una serie di canali di passaggio per i fluidi tra le piastre stesse.
L’intercapedine che si crea tra due piastre adiacenti costituisce il canale in cui scorre il fluido.
I fluidi caldo e freddo percorrono lo scambiatore a canali alterni in modo che una piastra sia sempre a contatto da un lato con il fluido caldo e dall’altro col fluido freddo.
In corrispondenza degli angoli della piastra ci sono i fori che permettono l’ingresso e l’uscita dei fluidi.
Una piastra può avere dimensioni che vanno dai pochi decimetri quadrati (100 mm x 300 mm di lato) fino a 2 o 3 metri quadrati (1000 mm x 2500 mm di lato).
Il numero di piastre per scambiatore va dalla decina fino a qualche centinaia, raggiungendo così aree di scambio fino a migliaia di metri quadrati.
La figura mostra l’andamento dei fluidi all’interno dello scambiatore.
I fluidi vengono suddivisi in più flussi paralleli e possono realizzare una controcorrente perfetta.
Flusso interno in un BPHE
La corrugazione viene ottenuta per stampaggio a freddo di lamiera con spessori da 0.3 a 1 mm.
I materiali più utilizzati per le piastre sono l’acciaio inossidabile (AISI 304, 316), il titanio e l’alluminio.
Le corrugazioni presenti all’interno della piastra impongono al fluido un percorso tortuoso e definiscono un la spaziatura tra due piastre adiacenti b, che può andare da 1 mm a 5 mm.
I fluidi possono attraversare i canali in serie (soluzione poco usata) o in parallelo realizzando configurazioni in controcorrente o equicorrente.
La configurazione in serie si impiega quando si ha una portata piccola per ogni fluido ma salto termico elevato.
Il problema principale è l’elevata perdita di carico e la non perfetta controcorrente.
La configurazione con canali in parallelo e in controcorrente viene usata per grandi portate con salti di temperatura modesti, ed è la più utilizzata.
Quando c’è una differenza elevata tra le portate (oppure tra il valore massimo delle perdite di carico ammissibili) dei due fluidi è possibile far percorrere lo scambiatore due volte dal fluido con portata minore (o che consente perdite più elevate) in modo da equilibrare i valori delle cadute di pressione o delle portate specifiche nei canali.
La figura illustra le diverse configurazioni di configurazione: in parallelo, in serie e mista.
Uno dei problemi più importanti per gli scambiatori a piastre è la disuniformità di alimentazione dei diversi canali in parallelo.
Infatti il fluido tende a distribuirsi in quantità maggiore nei primi canali rispetto agli ultimi in modo da equilibrare le perdite.
All’aumentare del numero delle piastre la distribuzione peggiora comportando una diminuzione delle prestazioni globali dello scambiatore.
Esistono due tipi fondamentali di scambiatori a piastre: i saldobrasati (BPHE-Brazed Plate Heat Exchanger) e quelli con guarnizione (PHE-Plate Heat Exchanger).
Scambiatore di calore a piastre con guarnizioni
Nei PHE le piastre vengono impaccate a pressione mediante testate e tiranti, la tenuta è garantita da guarnizioni. Le guarnizioni, oltre alla tenuta servono ad indirizzare i fluidi.
Le guarnizioni vengono alloggiate lungo dei solchi presenti sui bordi delle piastre.
Le temperature massime di utilizzo degli scambiatori a guarnizione sono comprese tra 80°C e 200°C mentre le pressioni possono arrivare a 25 bar
Le guarnizioni sono disponibili in vari tipi di gomme butiliche o siliconiche.
Le caratteristiche principali di questi tipi di scambiatori sono :
- facile e rapido smontaggio per operazioni di pulizia e controllo
- adeguamento a condizioni d’impiego variabili aggiungendo o togliendo piastre termiche per modificare il flusso termico installato
- le perdite di fluido dovute a non perfetta tenuta delle guarnizioni non vanno a contaminare l’altro fluido ma vanno verso l’esterno
- possibilità di utilizzo di materiali che mal si adattano alla saldatura, come il titanio - le guarnizioni limitano i valori della pressione e temperatura massima
- costi elevati a causa della progettazione degli stampi, presse e di tutto il processo produttivo
- costi elevati delle guarnizioni
Scambiatori di calore a piastre saldobrasate
Gli scambiatori di calore a piastre saldobrasate non hanno testate, tiranti e le guarnizioni di tenuta perché le piastre vengono saldobrasate in forno a temperature dell’ordine dei 1000°C.
In fase di assemblaggio viene messo tra le piastre un foglio di materiale brasante (generalmente rame ma anche nichel), il pacco viene pressato e successivamente messo in forno per qualche ora.
Lo scambiatore BPHE si presenta più compatto, leggero e meno ingombrante di uno con guarnizioni.
La figura mostra il percorso fatto dal fluido caldo e freddo.
La brasatura quindi assolve sia la funzione delle guarnizioni che quella del telaio.
In questi scambiatori generalmente vengono utilizzate piastre con corrugazioni a spina di pesce, le quali vengono assemblate alternando le direzioni delle corrugazioni in modo da creare il reticolo di contatto.
I punti di incrocio tra le corrugazioni di due piastre accoppiate formano un fitto reticolo di punti di contatto che conferiscono la tenuta in pressione e inducono dei flussi vorticosi che migliorano lo scambio termico.
In questo modo la turbolenza dei fluidi è elevata anche per basse velocità nominali di ingresso e il deflusso passa da laminare a turbolento per basse portate specifiche.
La figura mostra uno scambiatore sezionato avente 8 piastre totali (di cui 6 utili per lo scambio termico) in cui si vedono i 3 canali impiegati per il passaggio del fluido frigorigeno (in giallo) e i 4 impiegati per l’acqua (in blu).
Si nota subito che il percorso fatto dai fluidi è molto caotico, infatti la sezione di attraversamento varia continuamente .
Il principale svantaggio di questi scambiatori è che non sono smontabili per cui la manutenzione e la pulizia non sono possibili o perlomeno difficoltose, e la flessibilità non esiste nel senso che il numero di piastre non può in nessun modo essere variato.
Le piastre sono dotate di corrugazioni il cui scopo è quello di aumentare la turbolenza del fluido durante il deflusso nel canale.
La figura mette in evidenza i principali parametri geometrici della corrugazione: passo p della corrugazione, altezza b delle corrugazioni e l’angolo di inclinazione β rispetto la direzione principale del flusso.
L’inclinazione delle corrugazioni della piastra ha un effetto determinante sullo scambio termico e sulle perdite di carico, infatti un accoppiamento di piastre con angolo β elevato (>45°) conferisce una turbolenza e quindi uno scambio termico elevato pagati con una maggiore caduta di pressione.
Un angolo più piccolo (β <45°) conferisce al flusso minore turbolenza e minori coefficienti di scambio termico ma anche minori cadute di pressione.
La ricerca di un angolo β di compromesso tra elevati coefficienti di scambio e perdite di carico accettabili risulta quindi essenziale.
L’altezza delle corrugazioni b ha un effetto importante sui coefficienti di scambio perché una maggiore profondità provoca turbolenza maggiore.
L’altezza e il passo delle corrugazioni incrementano l’area di scambio della piastra : il fattore φ chiamato di allargamento della superficie è definito come
φ = area della superficie corrugata reale / area della proiezione della superficie corrugata
Nelle immagini sotto si vedono delle simulazioni Wieland Onda fatte su scambiatori a piastre di piccole dimensioni. Si vedono bene le linee di flusso che seguono l’angolo della corrugazione.
L’area effettiva è difficile da calcolare quindi per confrontare diversi scambiatori si fa riferimento all’area proiettata.
Bisogna tenere presente che scambiatori con uguale area proiettata (cioè piastre di uguali dimensioni) possono avere aree effettive diverse a seconda del valore del fattore di incremento φ .
Anche il rapporto tra lunghezza L e larghezza W delle piastre influisce sulle prestazioni ma in modo minore rispetto le altre variabili. In generale un rapporto elevato tra lunghezza e larghezza della piastra dà coefficienti di scambio elevati ma perdite di carico maggiori.
Evaporatore a fascio tubiero
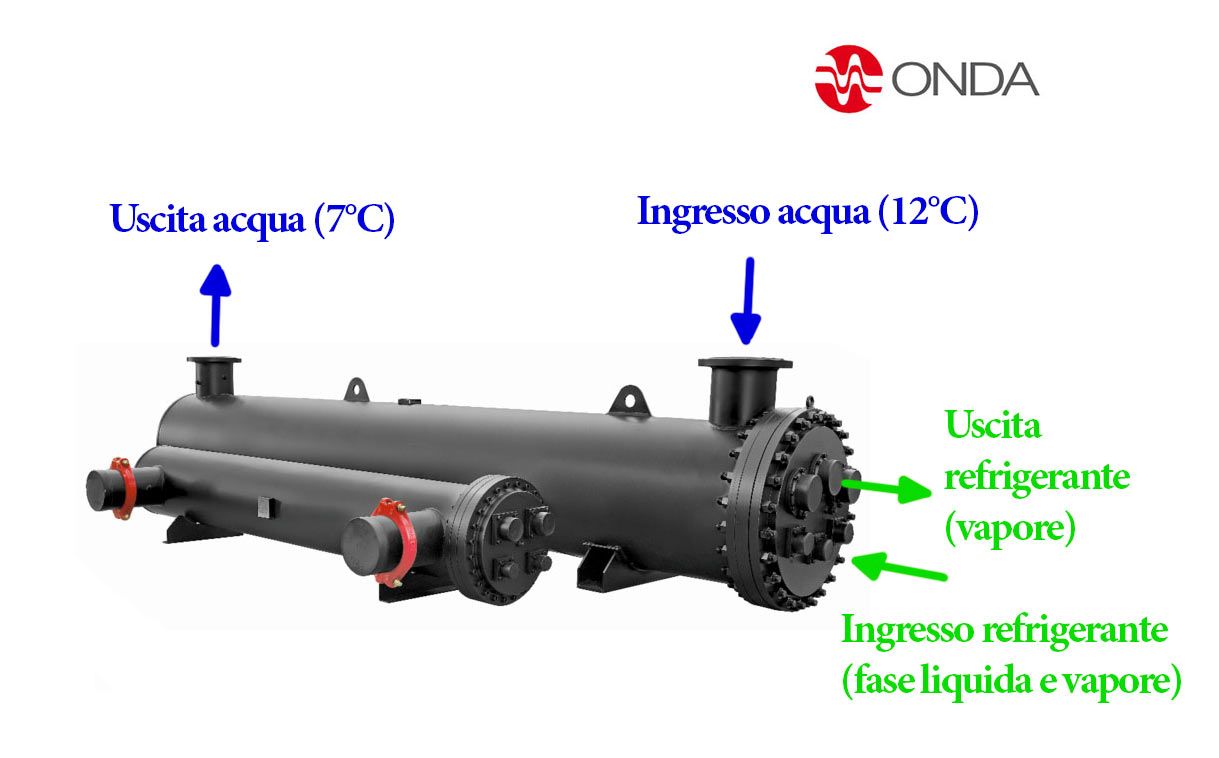
Evaporatori a fascio tubiero con tubi forcinati (ad U)
In un evaporatore a fascio tubiero l'acqua deve essere raffreddata generalmente da 12°C a 7°C utilizzando un fluido frigorigeno che evapora e cambia di fase, da liquida a gassosa. Generalmente la temperatura di evaporazione del fluido frigorigeno va dai 2 ai 4 °C.
Il refrigerante evapora all interno del tubo passando da liquido a gassoso e assorbe energia dall'acqua che si raffredda.
Negli evaporatori a tubi forcinati (serie Wieland Onda HPE, MPE, LPE) il refrigerante entra ed esce dallo stesso lato dello scambiatore, percorrendo la lunghezza dello scambiatore per due volte.
L'acqua invece passa esternamente ai tubi all'interno del mantello, e percorre lo scambiatore passando attraverso dei setti che fanno aumentare la lunghezza del percorso e la turbolenza.
Per avere più informazioni sugli evaporatori Wieland Onda clicca qui sotto :
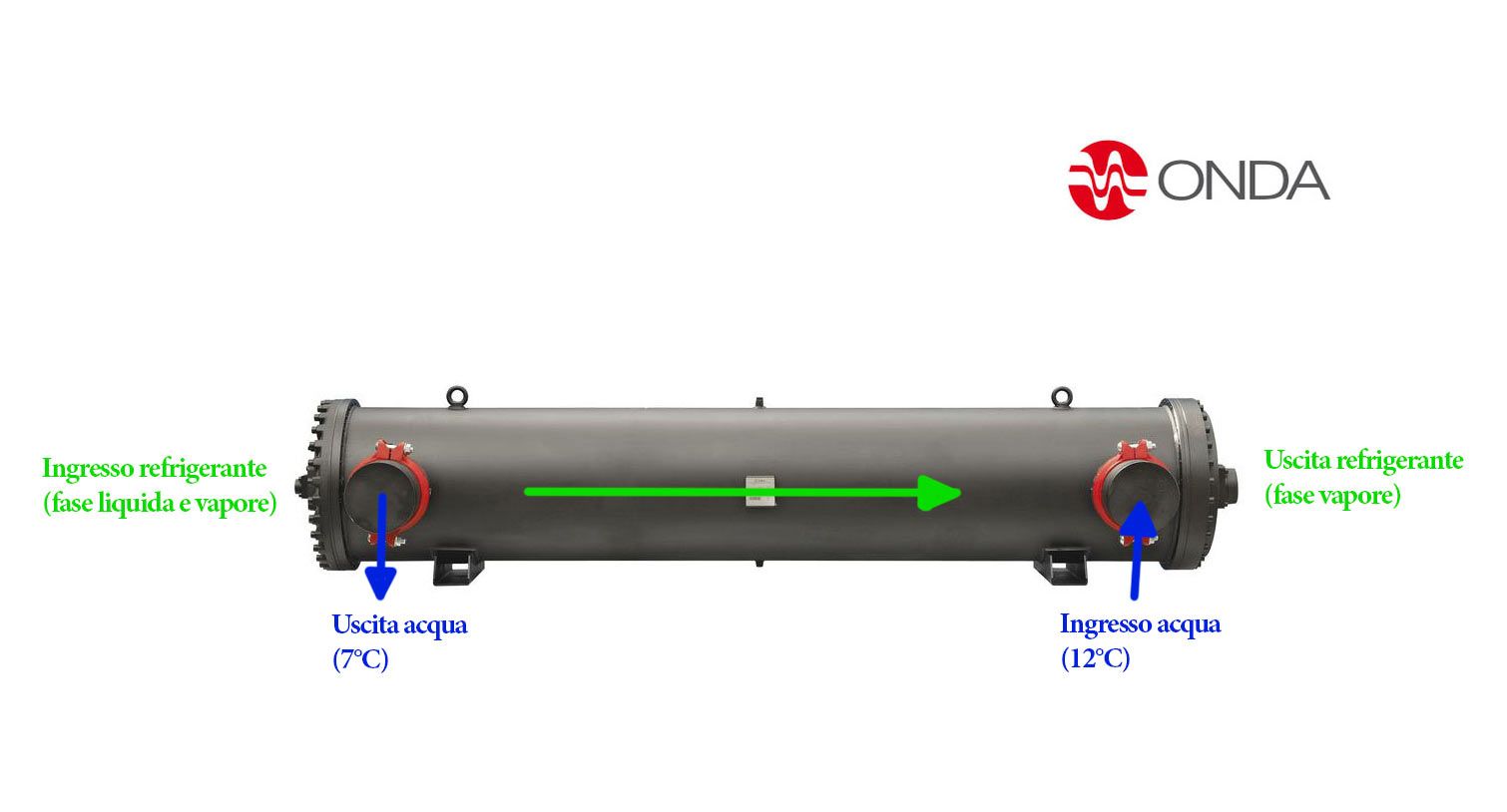
Evaporatori a tubi dritti monopasso
Negli evaporatori di ultima generazione invece, il refrigerante evapora percorrendo una sola volta la lunghezza dello scambiatore, in questo modo le perdite di carico del refrigerante all'interno dei tubi saranno minori.
Il refrigerante entra da un lato in fase liquida e vapore, evapora ed esce dal lato opposto in fase vapore anche surrriscaldato.
L'acqua si raffredda nel senso opposto in piena controcorrente.
Gli scambiatori Wieland Onda di questo genere sono gli LSE e gli SSE.
Per avere più informazioni sugli evaporatori Wieland Onda clicca qui sotto :
Hybrid Film Evaporator
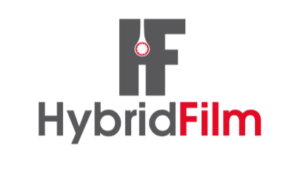
Vantaggi
Onda ha recentemente sviluppato un nuovo evaporatore a fascio tubiero innovativo ad alta efficienza e a bassa carica di refrigerante per rispondere a una crescente domanda del mercato, visti i continui aumenti del prezzo e delle tasse dei refrigeranti.
L'evaporatore "Hybrid Film" combina i vantaggi degli evaporatori allagati (alta resa) e quelli a falling film (bassa carica di refrigerante).
Il concetto di questo innovativo scambiatore di calore è stato sviluppato dall' R&D e testato nel laboratorio Wieland Onda con compressori ad olio e senza.
Il core design appartiene all'IPR di Wieland Onda ed è in attesa di brevetto.
Il nuovo sistema di distribuzione del refrigerante permette di avere il controllo del refrigerante attorno ai tubi in tutte le condizioni di funzionamento, sia a pieno carico che a carichi ridotti.
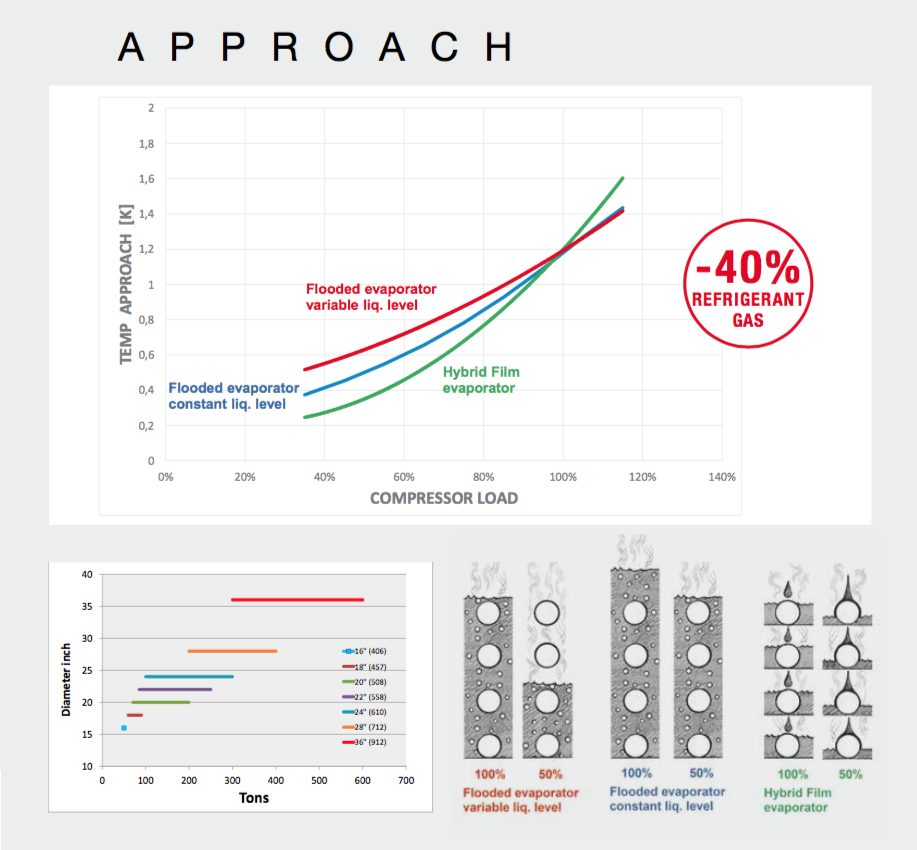
Approach
Quando il carico scende al di sotto dell'80% l'hybrid film funziona meglio di un equivalente evaporatore allagato con un approccio ridotto e quindi un impatto positivo sul chiller.
La carica di refrigerante rispetto ad un equivalente evaporatore allagato scende del 35-40 %
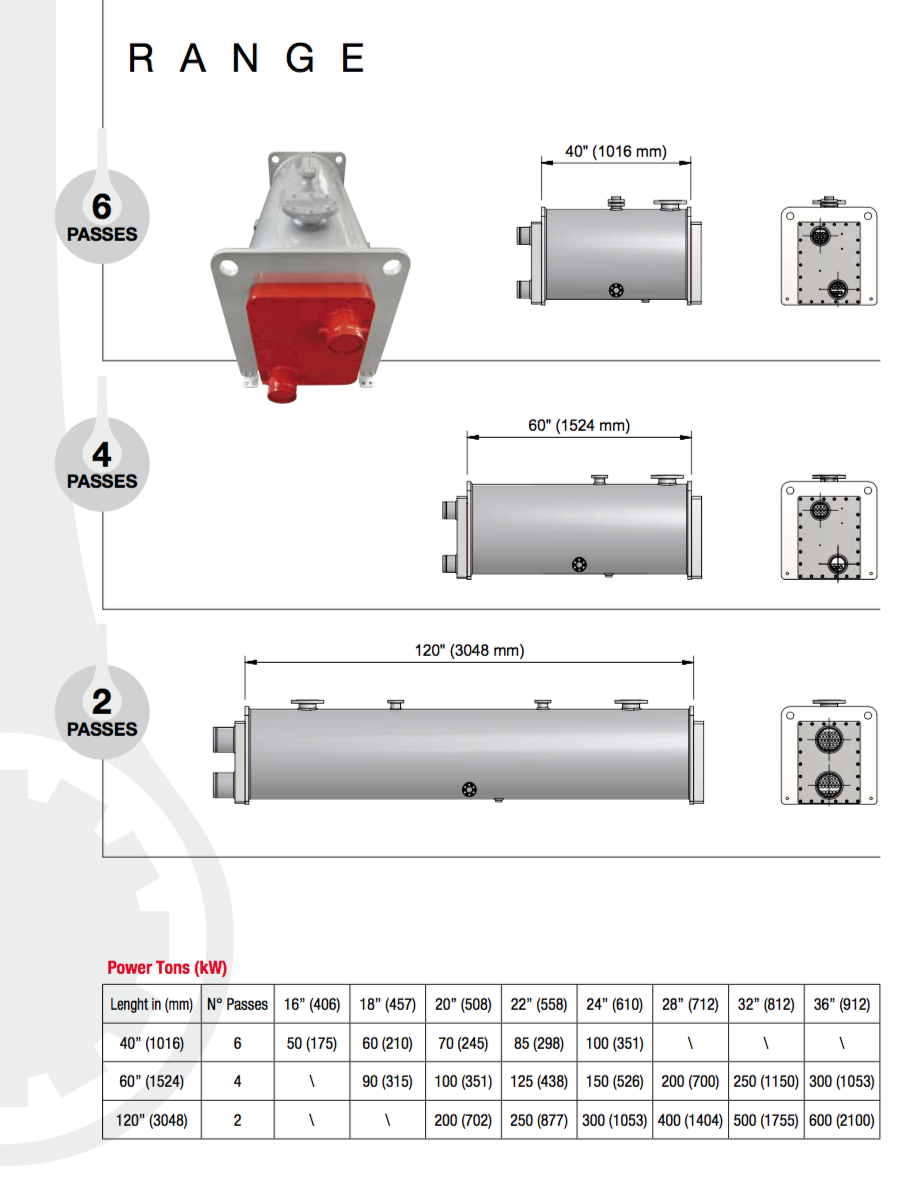
Per scaricare il catalogo vai al link qui sotto :
https://www.onda-it.com/ita/prodotti/scambiatori-di-calore-a-fascio-tubiero/hybrid-film-evaporator
Evaporatore allagato a fascio tubiero
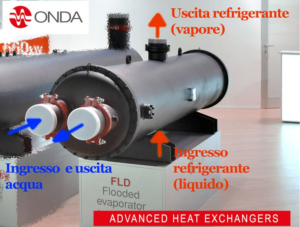
Il livello del liquido all'interno del mantello è controllato da un sensore che mantiene i tubi costantemente bagnati dal refrigerante.
In genere il mantello è solo parzialmente riempito di tubi, si dispone di un grande volume nella parte superiore in cui il vapore fluisce a basse velocità e si separa dal liquido.
Prima di uscire dallo scambiatore il vapore potrà passare attraverso un separatore di gocce per poi andare nel compressore.
Questi evaporatori sono generalmente utilizzati con compressori senza olio ed hanno una elevata efficienza.
I vantaggi maggiori rispetto agli evaporatori ad espansione secca sono i bassi approcci utilizzati (evaporazione a 5 °C) e quindi un più basso costo specifico in termini di euro/kW.
Per avere informazioni sugli evaporatori allagati Wieland Onda clicca qui sotto :
Scambiatori a piastre: Funzionamento Monofase - Evaporatore - Condensatore
Funzionamento scambiatori di calore a piastre : scambio termico monofase e bifase
Gli scambiatori di calore a piastre hanno lo scopo di riscaldare/raffreddare fluidi di processo (monofase ad esempio acqua, olio, glicole, ecc) oppure nel campo bifase quello di fungere da evaporatore o condensatore (utilizzando fluidi frigorigeni come R134a, R1234ze, R410A, ecc. ) in un ciclo frigorifero a compressione di vapore.
In questo articolo cercheremo di spiegare in modo semplice il funzionamento di questi tipi di scambiatori.
Nel caso di un processo monofase abbiamo due fluidi che entreranno nello scambiatore di calore generando uno scambio termico in perfetta controcorrente, quindi, l’ipotetica temperatura massima di uscita di entrambi i fluidi sarà pari alla temperatura di ingresso del fluido opposto.
Questo potrebbe avvenire solo se l’area di scambio tendesse all’infinito, quindi nella realtà questo non può succedere.
Vediamo quindi un esempio di flusso controcorrente monofase, in cui il fluido freddo entra e aumenta di temperatura asportando calore dal fluido caldo che va a raffreddarsi diminuendo di temperatura.
Nel caso invece di un evaporatore a piastre in genere lo scopo è quello di raffreddare un fluido di processo tramite l’evaporazione a temperatura costante di un fluido frigorigeno.
L’applicazione di gran lunga più comune è quella di raffreddamento di acqua da 12°C fino a 7°C per impianti di condizionamento dell’aria.
In questo scambiatore a piastre il fluido frigorigeno entra ad alta velocità in fase liquida (in realtà il titolo di vapore va da 0.2 a 0.3) e va ad evaporare attraverso lo scambiatore a piastre dal basso verso l’alto asportando calore al fluido che scorre controcorrente nell’altro lato (nelle piastre del canale opposto).
L’ultima parte dello scambiatore serve per surriscaldare il gas già evaporato in modo che non ci sia ritorno di particelle di liquido nel compressore per evitare rotture del compressore stesso.
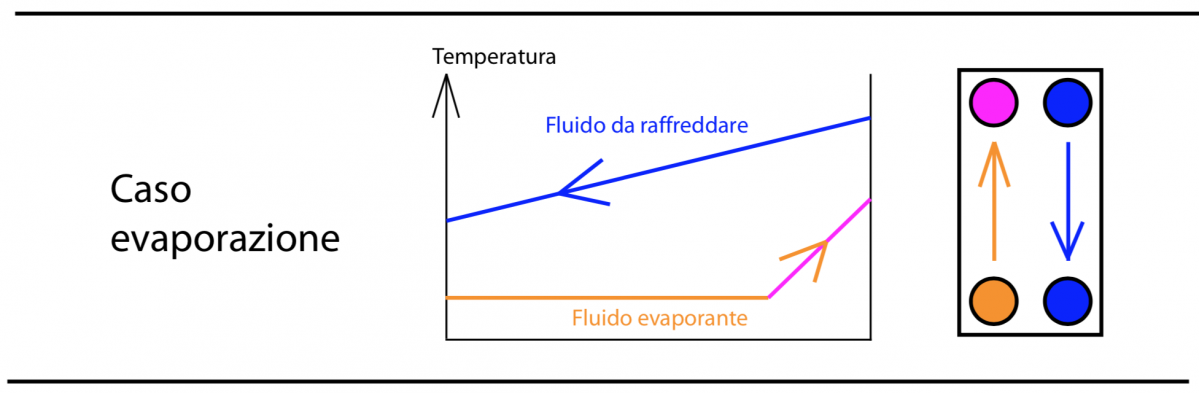
La parte più importante di questo processo per il corretto funzionamento dello scambiatore è la corretta distribuzione del fluido bifase all’ingresso dell’evaporatore in modo che tutte le piastre di scambio (lungo lo scambiatore) vengano alimentate con la stessa portata di gas.
Onda ha brevettato un sistema di distribuzione che permette al gas di distribuirsi omogeneamente lungo tutto lo scambiatore.
Come vediamo in figura si vede che una corretta distribuzione ha una zona di surriscaldamento del gas (in arancione) omogenea dall’inizio alla fine dello scambiatore.
Se la distribuzione non è omogenea avremo zone con vapore piu’ surriscaldato e zone con vapore meno surriscaldato, il funzionamento del chiller in questo caso può essere instabile.
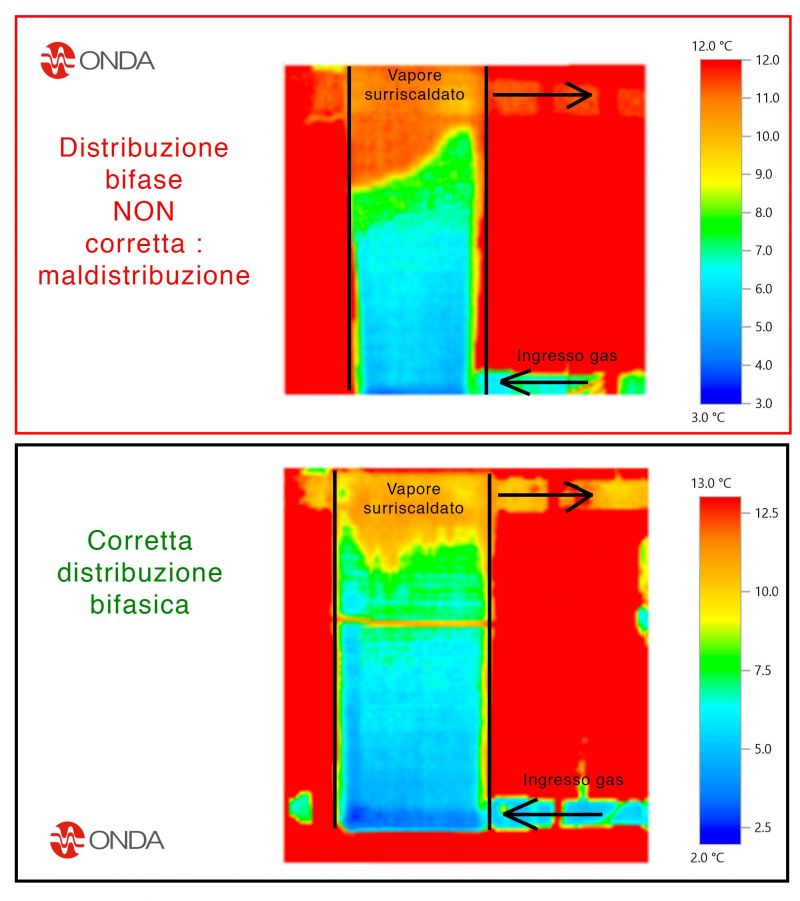
Nell’ultimo caso di condensazione abbiamo invece un fluido frigorifero in stato gassoso (generalmente ad alta temperatura 60-70°C) che deve condensare a scapito di un fluido che nell’altro lato dello scambiatore va a riscaldarsi.
L’ultima parte dello scambiatore serve a sottoraffreddare il condensato di alcuni °C, di solito 3-4.
In questo caso il gas surriscaldato entra in alto e scende attraverso le piastre di scambio condensando fino a diventare liquido uscendo in basso.
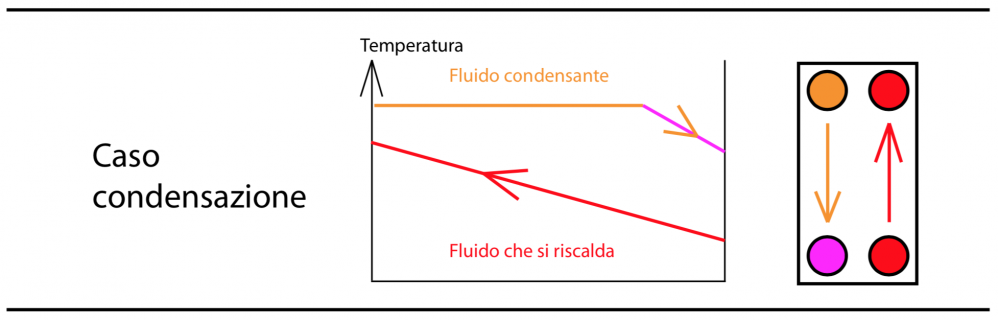
Per scaricare il PDF clicca il link sottostante
Enrico Golin
Wieland Onda Srl
Condensatore a fascio tubiero
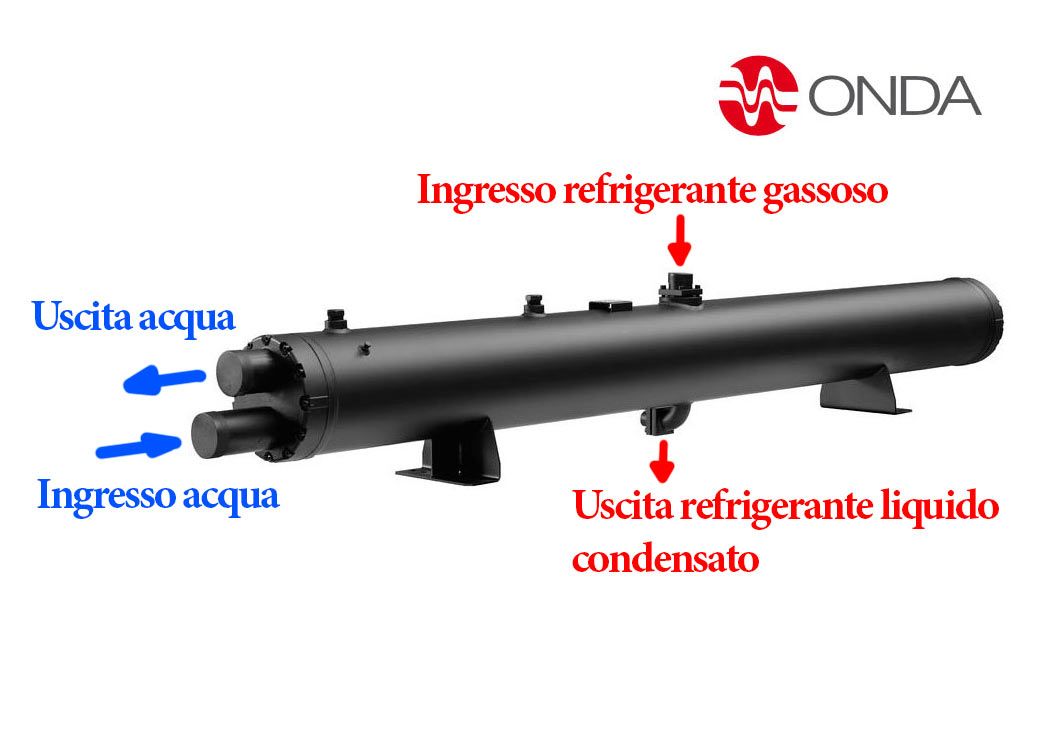
Condensatori a fascio tubiero
In un condensatore a fascio tubiero, il refrigerante gassoso (a volte surriscaldato fino a 80-90 °C in uscita dal compressore) deve essere condensato e riportato in fase liquida.
Generalmente la temperatura di condensazione va da 40 a 45 °C per applicazioni standard.
Per fare questo si utilizza dell'acqua che generalmente entra nello scambiatore a 25-30 °C e si riscalda fino ad un massimo di 35°C, assorbendo il calore di condensazione.
Il refrigerante entra dalla parte superiore del mantello ed esce nella parte inferiore in fase liquida (a volte sottoraffreddata).
L'acqua scorre dentro i tubi ed esce in genere dalla stessa parte, percorrendo la lunghezza dello scambiatore 2 - 4 - 8 volte (numero di passi).
Per avere informazioni sui condensatori Wieland Onda clicca qui sotto :